纳瓦拉大学(university of navarra)的研究生就业率在西班牙首屈一指,成为了高标准教育的典范,获得好成绩的原因之一是该校一直以来都鼓励学生尽可能多地参与实际项目。例如,纳瓦拉大学tecnun工程学院的学生会参加一年一度的大学生方程式赛车(formula student)工程大赛。
学生们利用从课程中学习的工程技能,与其他大学的团队比赛设计并制造一辆方程式赛车。在最近的一场比赛中,tecnun的主要任务是利用3d打印技术来提高汽车性能。团队很快就得出了结论:进气歧管的设计是决定成败与否的关键因素,也是可以通过3d打印技术来改进的地方。
但是,tecnun赛车技术总监javier aperribay表示,制造进气歧管可不简单。“进气歧管的设计非常复杂,它包含好几个关键组件,这些组件对四个进气歧管的空气分布至关重要,”他解释道。
复杂进气口设计的3d cad渲染,包含多个单独的组件
打破传统制造方法的限制
团队选择使用碳纤维复合材料制造进气歧管,以减轻重量并降低油耗。通常,制造这样的部件需要一个模具来铺叠复合材料,然后才能制造出最终零件。cnc加工生产铝制模具可以是一个选择,但这种工艺通常灵活性低且成本高昂。后续的任何修改都会拖慢项目进度并增加额外成本。
采用传统方式生产铝制模具需要两个月的时间,因为时间紧迫,也无法对模具进行任何迭代,团队意识到,这将会限制他们设计进气歧管。
化繁为简
为支持这所大学,当地stratasys经销商pixel sistemas赞助了该团队,为学生们制作了fdm可溶解消失模具。
他们使用stratasys fortus 450mc™ 3d打印机搭配st-130™可溶解消失模具材料进行3d打印,然后在外部包覆碳纤维复合材料,从而制造出进气歧管的模具。固化后,洗掉内部的可溶解消失芯,便可以留下最终的复合材料零件——这是制造复杂形状的理想工艺。
在进气歧管的生产过程中使用stratasys fdm可溶解消失模具,让我们能够使用碳纤维材料来取代笨重、低效的材料,与铝制模具相比,st-130材料可溶解特性非常出色,能实现更复杂的进气歧管形状。进气歧管的第一个模具在5小时内就通过3d打印完成制作,而传统铝制模具需要三周才能交货。
——javier aperribay
tecnun赛车技术总监
该团队还指出,在固化过程中,这种材料能够经受121°c的高温,在某些温度下,其承受的压强能高达620kpa。
加快生产速度,留出优化时间
该团队利用在生产过程中节省的时间来改进设计,最终的碳纤维进气歧管比使用传统方法制造的歧管轻60%。为了检验这一成果,tecnun团队参加了两场国际大学生方程式赛车比赛,取得了迄今为止最好的成绩。团队也在计划参加更多比赛,毫无疑问,fdm可溶解消失模具是克服工程挑战的一项利器。
制作完成的碳纤维进气歧管表面非常光滑,增加了气流并提升了赛车在赛道上的表现
源文摘自:stratasys
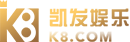
服务热线:0755-82953613
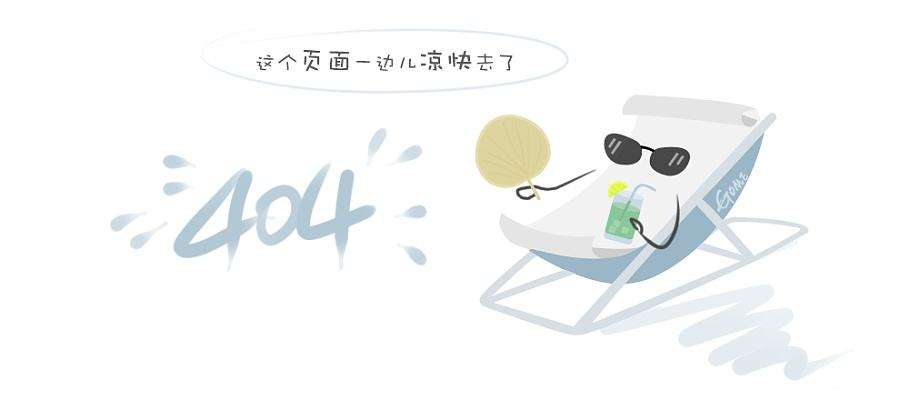
关注普立得
-
-
服务热线:
0755-82953613 -