速度与质量并重
plyform s.r.l位于意大利的瓦拉洛蓬比亚,在利用先进复合材料制造工业应用零件方面堪称专家。该公司涉猎众多工业领域,在航空航天领域的专业经验尤为突出。事实上,plyform是意大利飞机结构件的主要供应商之一,以制造优质的复杂复合结构件而闻名。
为了不断提高响应客户的能力,plyform需要一种生产凯发k8官网的解决方案来减少时间和成本,同时让plyform保持创新。
对于传统的复合材料生产而言,其最大的挑战是缩短交付时间、降低成本,以及最终复合材料零件的质量。
——luca ceriani
plyform制造工程主管
在f900™工业级3d打印机上,使用ultem™ 9085树脂材料,3d打印直升机内把手
3d打印带来积极影响
为了实现目标,plyform研究了多种工业级增材制造凯发k8官网的解决方案,并深刻认识到工业级3d打印能够为他们带来的益处。该公司选择了stratasys基于fdm®技术的的f900™3d打印机。f900让plyform能够使用3d打印复合材料模具,为直升机生产多种高质量的碳纤维零件,相比铝制模具,速度明显提升且成本大幅降低。
这些优势在生产飞行员的周期操纵杆(又称“驾驶杆”)时得到了印证,该公司使用高性能可溶性材料st-130 3d打印了一个模具,然后将碳纤维复合材料包裹在模具周围,固化后,洗掉内部的可溶解消失模,便可以留下最终的复合材料零件。
如果采用传统工艺来生产直升机飞行员操纵杆的复合材料模具,我们需要四个小时来铣削模具,再用四个小时进行外部处理以避免树脂污染,有了stratasys fdm 3d打印机,我们可以在2.5小时内3d打印出一个模具,同时将成本降低80%。此外,这项技术让零件质量提高了约30%,这彻底颠覆了我们的业务模式。
——luca ceriani
plyform制造工程主管
与传统制造相比,只花了一半的时间就制作出飞行员周期操纵杆最终复合材料零件,且成本降低了80%。
提升能力与服务
3d打印技术带来了显著的成效。如今,从复合材料模具到最终零件生产,plyform将f900用于其整个生产流程中。随着越来越多的客户要求在短时间内交付小批量的最终飞机零件,plyform也在利用f900提升其服务客户的能力。
由于航空航天行业具有严格的认证要求,plyform利用stratasys的航空航天级材料ultem™ 9085,可生产直接用于飞行的零件,这些零件满足飞机防火、防烟雾和防毒的要求。
plyform发现,使用3d打印的复合材料模具而制成的直升机周期操纵杆的碳纤维芯轴,与传统复合材料生产工艺相比,质量提高了30%。
我们可以利用增材制造技术来解决传统航空航天小批量生产在时间和成本上的难题,但该行业有着极其严格的认证要求,生产的每一个零件都必须具备最高水准的可重复性和可追溯性,在我们尝试过的所有增材制造技术中,f900提供了最佳的精确度和可重复性,同时,ultem™ 9085树脂符合fst(防火、防烟雾和防毒)要求并具有出色的耐热性和耐化学性,是航空航天业的理想材料。通过这项技术,传统模具制造工艺不再是必须,我们能以更低的成本,按客户的需求,3d打印轻量化零件。
——luca ceriani
plyform制造工程主管
plyform利用f900的大型打印托盘,可以生产复杂的几何形状部件,从极小的毫米型零件到大型零件,这可能是减材制造工艺无法实现的。通过3d打印机的功能和增材制造工艺,plyform能够满足自身和客户的长期需求。
源文摘自:stratasys
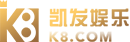
服务热线:0755-82953613
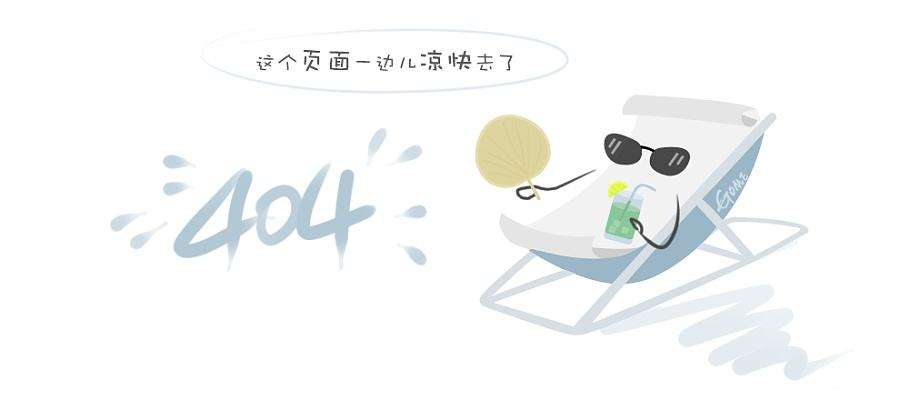
关注普立得
-
-
服务热线:
0755-82953613 -