dmg mori是金属切削制造设备的领导者,一个多世纪以来一直生产高质量的 cnc 机床。在过去的 20 年中,dmg mori 一直在投资于增材制造、自动化和数字化等未来领域。
该robo2go第二代机器人系统不可或缺的工厂自动化产品。机械臂配备两个独立的抓手,可一次从多达四个 cnc 系统装载和卸载零件,同时采用智能概念来增强人机之间的协作。
工厂车间的 dmg mori robo2go 第二代系统。重新设计的部分是将两个末端执行器连接到机械臂的头部。(来源:dmg mori)
additive intelligence是 dmg mori 的增材制造设计咨询公司,与内部和外部客户合作。该团队的任务是为金属增材制造重新设计 robo2go 系统的笨重机器人头部。
dmg mori 的工程师通过将拓扑优化与场驱动设计技术和先进的晶格结构相结合,彻底改革了这一关键部件的设计。
“借助 ntopology,我们能够创建强大而独特的增材设计。使用传统的 cad 系统不可能创建这样的组件。”dmg mori 增材制造项目工程师 martin blanke
在本案例研究中,我们深入探讨了 dmg mori 工程师遵循的设计流程。您将了解他们如何利用 ntopology 的独特功能来简化流程并获得优化的结果。
设计挑战
robotgo 2nd gen 已经是一个非常成功的产品。然而,为了改进他们未来几代机器人系统的初始设计,dmg mori 希望提高机器的精度并节省宝贵的制造和装配时间。
原始装配包含79 个单独的零件,这使得公差、精度和装配成为一项具有挑战性的任务。此外,该组件的刚度和重量限制了整个系统的精度和最大负载能力。
该项目的主要目标是开发一种轻量化设计,其外形与原始组件相同,但组件数量和重量有所减少。在实践中,实现这一目标意味着找到一种方法来保持原始结构轮廓,同时从内部去除尽可能多的材料。
原始 robo2go 头部(左)和重新设计的组件(右)。
设计方法论
在设计过程的早期,martin blanke 和他的团队决定采用可变外壳和格子作为减轻原始设计重量的最佳方法。但是,使用传统的 cad 工具几乎不可能及时执行这些任务。
martin 指出,“使用我们的传统 cad 系统,只能以 2 或 3 毫米的恒定厚度对该组件进行外壳处理,但我们在 ntopology 中找到了我们的凯发k8官网的解决方案。”
设计过程概述。原始设计的表面首先在 cad 中进行颜色编码,然后导入到 ntopology 进行轻量化和优化。
ntopology 的场驱动设计功能帮助他们克服了这一瓶颈。以下是他们遵循的过程的概述:
- 首先,他们在 cad 中对原始设计的所有表面进行颜色编码。每种颜色对应一个不同的子系统。后来在 ntopology 中用作输入参数来确定每个部分的厚度。
- 然后,他们在 ntopology 中导入 cad 文件并在将它们组合成一个实体之前对每个部分进行外壳化。外壳的厚度由拓扑优化驱动,以最大限度地提高其刚度。
- 最后,他们用共形晶格填充内部体积,以增加零件的结构强度并为增材制造创建支撑结构。使用 ntopology 的工程仿真工具,他们快速迭代以选择最佳晶格。
带有颜色编码的设计自动化
dmg mori 的工程师不仅设计了一次性的轻型部件,还开发了一种稳健且可重复使用的优化流程。他们的可重用工作流程基于导入的 cad 主体的颜色编码表面。
颜色编码使工程师能够在 ntopology 中自动选择相关曲面,并开发强大且可重复使用的设计工作流程来加速他们的设计过程。
首先,团队在外部 cad 系统中为每个子系统的表面定义颜色:蓝色代表气动入口和出口,黄色代表气动通道,红色代表与机器人的接口,紫色代表安装点,绿色代表接触面,和白色的外表面。
然后,他们使用 ntopology 中的颜色属性来选择相关曲面并开发可重复使用的工作流程。如果输入几何在未来的迭代或其他项目中发生变化,团队只需导入新的 cad 文件,优化过程就会自动重新运行。
可变壳的拓扑优化
一个基本的设计要求是原始设计的外部形状因素需要保持不变。相同的限制适用于与手臂和末端执行器、气动系统的入口和出口、电子设备的安装螺钉和电缆孔的接触点。
拓扑优化不能直接用作最终设计。然而,该团队使用拓扑优化结果来驱动外壳的厚度。
拓扑优化结果推动了可变脱壳操作的厚度。
使用颜色编码系统,martin 的团队自动定义了拓扑优化的设计空间。然后,将优化过程结果用作输入以创建可变厚度的外壳:需要更多材料的地方更厚,不需要的地方更薄。
“使用 ntopology 的一大优势是可以将拓扑优化的结果转换为有用的模型,该模型可以直接或间接用于其他功能。”dmg mori 增材制造项目工程师 martin blanke。
这个过程帮助他们在不改变零件外观的情况下掌握了拓扑优化的一些结构优势。
多系统集成和功能整合
一旦外壳准备好,结构和气动系统也需要轻量化并集成到设计中。
外壳、加厚的功能表面和气动通道使用布尔联合连接成一个整体。
使用颜色编码系统,martin 的团队可以轻松地为每个子系统应用不同的恒定壳厚度。例如,气动入口和出口的厚度大于气动通道。使用传统 cad 工具执行此操作几乎没有那么简单。
该过程的最后一步被 martin 认定为“使用 ntopology 的主要优势之一”。一旦生成了单独的外壳,就可以使用简单的布尔联合将所有内容组合成一个单一的主体。布尔联合块将多个隐式实体合并为一个,并在它们之间进行可选混合以添加圆角。
用于刚度和支撑的共形点阵
在这个阶段,许多内部特征具有无法使用金属增材工艺制造的大悬垂物。通常,支撑结构用于3d打印此类部件,但它们的移除非常繁琐且浪费材料。
工程团队使用晶格结构为零件的所有内部区域提供永久支撑。此外,这种内部晶格结构增加了零件的刚度。
内部共形晶格与外壳连接以形成最终设计。
为了确定最佳晶格厚度,该团队利用了ntopology 的集成仿真工具。此功能使他们能够在 ntopology 中自动运行多个 fem 和晶格模拟,快速评估结果并更改特定参数以迭代和优化其设计。
该软件的集成工程仿真和设计自动化功能为 martin 的团队节省了许多工程时间,因为迁移到不同的软件只会增加工作流程的复杂性。
最后的润色和制造
设计现已完成,只需要添加一些最终细节即可为制造和后处理做好准备。
例如,最终模型中的孔洞和空心区域可能会导致增材制造过程中出现缺陷。martin 和他的团队用坚固的材料填充了大部分这些部分,这些材料随后可以很容易地进行 cnc 加工。
最终设计是使用额外的胶印材料进行 slm 3d 打印,然后使用 cnc 加工完成。
在lasertec 30 dual slm系统中进行 39 小时的金属增材制造并在dmu 50 5 轴 cnc 机床上进行精加工后,该团队终于有了新的轻量化设计的四个物理原型,可以进行测试并投入使用。
下一步
目前,dmg mori 的工程师正在机器人系统组装中测试这个新部件。目标是在 2022 年初实现商业生产。
早期测试表明,新组件更高的刚度重量比有助于将机器人系统的处理精度提高 16 倍。该团队计划在 ntopology 中应用类似的方法来轻量化其他类似的组件。
“牢不可破的几何形状、可重复使用的工作流程和模拟驱动的设计是增材制造设计的极其强大的方式。”dmg mori 增材制造项目工程师 martin blanke。
源文摘自:ntopology
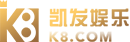
服务热线:0755-82953613
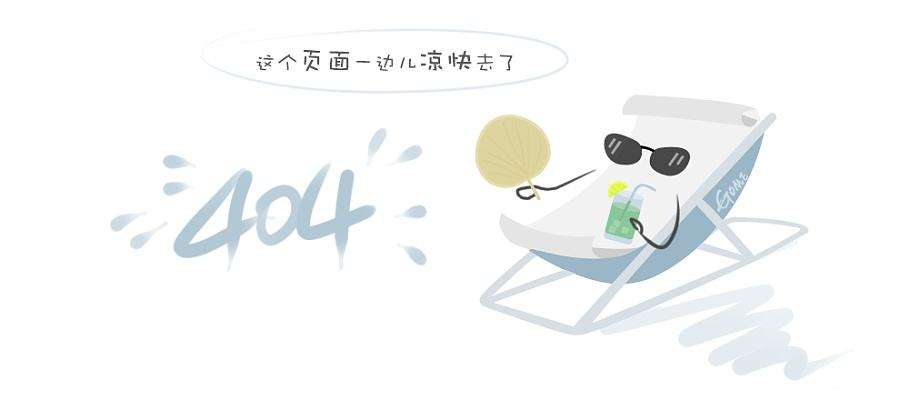
关注普立得
-
-
服务热线:
0755-82953613 -