案例分享丨解放双手与大脑,3d打印技术成功运用于汽车制动管检具生产-凯发k8官网
早在2010年,第一辆由3d打印而成的汽车urbee正式诞生,标志着增材制造技术在汽车领域的突破性应用。3d打印可以使金属零件的力学性能和精度达到锻件指标,保证汽车零部件的精度和强度要求。如今越来越多的汽车制造企业已将这一技术渗透于造型、设计、试制和试验的全过程,大大降低了研发成本、缩短了生产周期。
当然,不同于大多数汽车制造企业选择将增材制造技术用于打印汽车零部件,汽车零部件企业则将目标放在了工装夹具和检具上,相较传统方法3d打印技术同样提供了更加经济、高效的创新凯发k8官网的解决方案。
近日,广西柳州荆大汽车制动管制造公司就通过形优科技采用stratasys 的f370打印机成功打印出符合不同车型制动管检验需求的相应检具。
f370隶属于stratasys f123系列,是一款适用于办公室生产和原型制作的工业3d打印机。强大、实惠的快速原型制作专业凯发k8官网的解决方案不但易于操作和维护,适用于各种经验水平的用户,而且还能够灵活应对各个原型制作阶段,从概念验证到设计验证再到功能性能,支持 pla、abs-m30、asa 和 pc-abs 等多种材料。
全球知名汽车品牌奔驰公司就曾引入stratasys f370 3d打印机进行工装夹具的验证开发,并计划在未来将3d打印技术进一步应用于汽车零件设计辅助、异性卡尺、异性测量工具和质检工具等环节中。
柳州荆大公司生产的汽车制动管种类繁多,以每种车型至少需要6种不同类型的制动管(多者高达8种)来计算,所有车型的制动管种类超过60种。为确保制动管的精确度就需要对多个弯曲点进行检测,传统量具难以快速测量。
相较原本使用的cnc技术,3d打印首先将二维数据转换为三维数据,30cm左右的检具半天可完成设计、300cm尺寸的检具也只需2天便可完成设计。
随后使用stratasys的f370进行一体或分段打印,无需额外粘接方式便可固定在基板上完成制作。
得益于f370将强大的fdm技术与“从设计到打印”的grabcad软件相结合,无需专人维护便可便捷地将原始cad数据直接导入3d打印机立即开始打印。
同时,凭借极高的设备稳定性,f370 3d打印机可7×24小时无间断工作,不会出现堵头或脱离平台等常见造成打印失败的问题。
且打印仓内部有监控摄像头,支持以太网连接或wi-fi连接,可以通过智能手机、平板电脑远程查看打印进程,让3d打印机随时处于掌控之中,不需要人员对设备值守。
在细节设计上,f370 3d打印机也有不少“过人之处”。整个打印仓为全封闭设计,打印仓门的密封圈,确保打印仓内任何一个位置恒温工作,也便于模型均匀冷却。使用其打印的汽车制动管检具尺寸精度高,不会出现收缩变形情况,且各台设备打印一致性很高,方便后续的检具模块拼接。f370的抽屉式耗材仓拥有四个槽位,两个用于3d打印主体材料、两个用于qsr支撑材料。自动进料设计可大大减少操作时的查看和等待时间。
“有了 stratasys f370 的帮助,我们的检具生产效率得到极大的提高,无需配备周转器具,也为生产现场释放了更多空间占用。相对于传统cnc加工技术,在当前经济形势下为我们的企业有效降本增效。
— 柳州荆大公司”
可以说,stratasys f370 3d打印机的人性化设计大大提升了设备的自动化程度,让设计师、工程师可以无需为3d打印质量或进度而担心,真正解放了操作者的双手和大脑,让他们更好地聚焦于创造力的释放。
源文摘自:stratasys
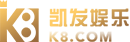
服务热线:0755-82953613
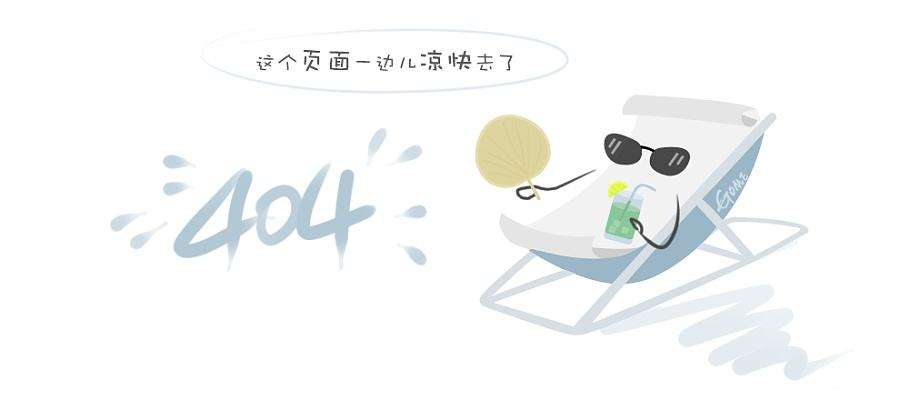
关注普立得
-
-
服务热线:
0755-82953613 -