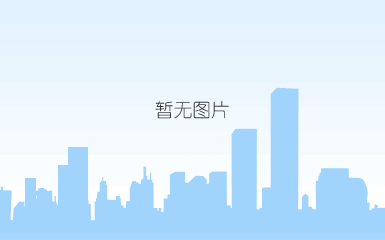
产业应用
普立得科技成立于2004年,专注于工业级3d列印与3d扫描逆向工程,并提供3d打印、三维扫描的代工整合服务,同时也代理德国知名品牌zeiss 三维扫描仪。
普立得科技在台湾地区设有3个区域办事处,大陆地区设有8个区域办事处,截至目前销售超过900套设备。普立得科技的3d打印/3d扫描技术正在改变和加快亚洲地区设计和制造的发展。 3d打印技术的出现是对生产方式的一种革新,客制化的特性能够为复杂设计降低成本,同时也能提供更低成本的零部件,使企业降低成本、获取更高利润。

boom的3d打印飞机部件揭示了制造业的未来
boom是如何利用3d打印来优化机库的性能和效率的? 3d打印技术已经席卷了世界制造业。从消费品设计到医学建模,越来越多的公司看到了3d打印在快速原型设计和制造方面的价值。 也许没有哪个行业能像航空航天那样产生如此深远的影响。波音公司预计通过在787梦想客机上3d打印钛部件,每架飞机可节省300万美元。霍尼韦尔通过增材制造节省了7个多月的重新设计时间。空中客车公司能够在头顶储物舱中制造出比以前轻15%的隔板。 boom两年多前开始使用3d打印,这是与全球领导者stratasys合作的一部分。从那时起,该公司已经制造了数百个3d打印零件、工具和原型,并节省了数千小时的工作时间。stratasys和boom最近宣布将凯发k8官方首页的合作伙伴关系延长七年至2026年,并将继续为复杂问题实施创造性凯发k8官网的解决方案。 boom和许多类似公司的利益是深远的。三个最显著的好处包括节省时间、金钱和体重。许多飞机零件固有地具有复杂的几何形状,部分原因是空间和重量限制。在3d打印之前,复杂的零件是从一块实心材料中铣削出来的,通常会变得极其昂贵、费力和耗时。 3d打印对boom的影响有多大?我们分享了五种独特的印刷部件,这些部件照亮了飞机制造的未来: 压力调节器支架 该压力调节器支架用于安装前起落架舱液压系统中调节备用压力的部件。如果这个部件是按传统要求用铝制成的,则需要6周以上的时间,成本为2000美元。这件飞行硬件只花了9.5个小时的打印时间,材料成本为70美元。 遥测连接安装 该部件在遥测连接验证测试期间用作设备支架。作为测试的一部分,工程团队在科罗拉多州14000英尺的派克峰上安装了设备,并确认可以在200英里外保持飞机和地面站之间的可靠遥测连接。 飞行控制试验台 该飞行控制试验台用于测试水平尾翼执行器偏转的机制,能够以极低的费用进行快速彻底的安全测试。尽管这些印刷部件不会用作飞行硬件,但它们使工程师能够确保飞行硬件执行器按预期工作。 压缩机排气管 快速原型设计的另一个很好的例子是,这种压缩机引气管道在发动机测试期间被用来重新引导发动机核心的空气,并作为测试件来确保飞行过程中的最终零件配合。如果没有3d打印,像这样的零件可能会失去特色,这一过程需要使用许多不同的零件才能获得最有效的形状。 这个传统的铝制零件的设计要复杂得多,大约需要4周和4000美元。对于boom来说,这部分只需要14个小时和150美元。 装满飞行硬件的托盘 这项94小时的打印工作由70多个零件组成,是在stratasys f900机器上完成的,机器上有一个装满飞机上各种系统飞行硬件的托盘。得益于电气、机翼、飞行控制、液压和机身系统,与传统制造方法相比,仅这一项工作就节省了数千美元和数周的交付周期。 随着越来越多的公司继续采用3d打印作为制造凯发k8官网的解决方案,boom继续寻找新的、创新的方法来使用这项多功能技术。随着该公司致力于建造历史上最快的商用客机overture,飞行部件、工具和原型的3d打印将发挥强大作用。
了解更多
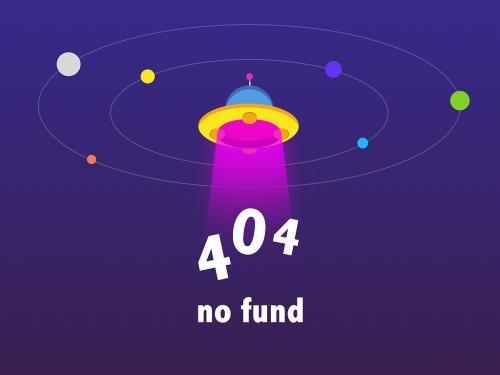
3d打印——飞行的未来
对于建造xb-1的团队来说,3d打印在建造的每个阶段都被证明是无价的。 强大的发动机。强金属。坚固的起落架。 当我们想到飞机零件时,我们想象的是几乎坚不可摧的材料和组件。3d打印的零件不会出现在脑海中。但材料和3d打印机的进步正在加速变革,使3d打印成为原型设计、工具和飞行硬件的完美选择,更不用说更换零件、内饰甚至厕所固定装置了。 3d打印正在改变我们设计和制造飞机的方式。 对于建造boom超音速演示机xb-1的团队来说,3d打印在建造的每个阶段都被证明是无价的。飞机上安装了300多个独特的零件。但3d打印对xb-1的贡献远不止零件制造。 三台3d打印机,三种需求 在xb-1构建的早期,boom团队与stratasys合作,探索3d打印(也称为增材制造)的选择。该项目着眼于3d打印,以满足三种不同的需求:功能原型、工具支持和飞行硬件的按需制造。三台打印机满足了建造的需要:stratasys f900、450mc和f370。 f900、450mc和f370。 stratasys f900是一架机器的战马,在boom的机库中占据了中心舞台。f900打印多种材料,包括ultem 9085和ultem 9085cg。两者都是阻燃、高性能树脂热塑性塑料,具有高强度重量比、优异的耐热性和高冲击强度。该团队使用9085打印钻头块,并使用9085 cg打印已经安装在xb-1上的数百个零件。9085 cg具有合格证书,与标准材料相比,具有更好的可追溯性和过程控制,是飞机零部件制造的理想选择。 stratasys fortus 450mc还可打印多种材料。该团队指定它用于用fdm尼龙12 cf打印钻头块,这是一种非常坚固的材料。fdm尼龙12 cf浸渍有碳纤维,是打印硬质钻头的理想选择。在xb-1钛合金后机身的建造过程中,该团队使用了数百个钻块,连夜打印。它不仅加快了构建速度,还减少了团队的停机时间。 stratasys f370通常使用asa打印,这是一种经济、低强度的材料,非常适合快速成型和测试配件。该团队用f370打印了原型,以减少任何意外碰撞(零件干扰或零件连接或接触的不匹配区域)的风险,并安装到现有的飞行硬件上。3d打印零件的测试配件支持设计改进,因此当团队最终制造零件时,每个零件都像手套一样合身。 功能原型:设计完美配合 在xb-1建造的第一阶段,首要任务之一是制造飞行控制系统的原型部件,包括机构和机械部件。每个原型的目标是验证零件是否适合,以及是否与其他零件一起工作。有了原型,团队可以在投入宝贵资源制造零件之前检查是否存在冲突(连接零件不匹配)。 stratasys f900是一款能够打印多个 通过在几个小时内打印多个迭代并微调设计,该团队保持了构建的进度。他们还避免了当零件从制造商那里到货时出现不合适的情况。通过将这些功能保留在内部,团队将停机时间降至最低。 stratasys f900是一款能够在其巨大的3'x2'x3'打印床上打印多个零件的机器。 所有的打印机都投入到制作从燃料歧管到发动机支架的原型的工作中。例如,该团队3d打印了外侧发动机前支架,以检查与左右发动机的配合情况。经过多次迭代,他们在配合检查中成功验证了设计。 此引擎的多次3d打印迭代 该团队为遮篷3d打印了这个原型闩锁机构,以确保运动学符合预期。 工具:实现更高的精度并减少潜在的损坏 在xb-1的建造过程中,该团队利用f900和450mc的能力打印了550多个钻头块。这些块支撑着钛机身与其他印刷夹具的精心组装,包括驾驶舱舱壁的夹具。 该团队使用计量学方法用这些块钻孔,从而提高了精度。该团队以更高的准确性减轻了对飞机的潜在损坏。 通过使用3d打印的钻块,该团队保持了建造进度,同时也减轻了钛制后机身的任何潜在损坏。 如果没有3d打印,钻块的交付周期将在几周左右,更不用说用铝制造数万美元了。通过内部3d打印,这些相同的块只需几天就能以更低的成本打印出来。 此图显示了团队使用3d打印的钻头块精确钻孔的许多地方. metallics:承受热量的钛3d打印零件 由于行业的重大进步,现在几乎可以使用任何材料进行3d打印。银、光聚合物、立体光刻材料(环氧树脂)甚至钛都可以应用于3d打印。 boom与velo3d建立了合作关系,生产金属零件,否则需要数周甚至数月的时间才能加工。该公司总共为xb-1 3d打印了21个零件,包括xb-1的一些最复杂的钛零件:可变排气阀(vbv)系统的歧管,该系统从发动机压缩机中排出多余的空气。 在vbv歧管的情况下,使用机械加工、焊接或铸造等传统制造方法是不切实际的。他们只能使用3d打印实现所需的零件几何形状。 boom与velo3d的合作使xb-1上安装了21个3d打印金属零件。 轻型3d打印零件:航空航天工程师的游戏规则改变者 3d打印不仅在建造过程中节省了时间和资源,还减轻了飞机的重量——这改变了所有航空航天工程师的游戏规则。由于飞机重量与燃料消耗直接相关,航空航天工程的目标是制造一种重量轻、同时满足所有安全要求的飞机。重量越轻的飞机燃烧的燃料越少,因此重量的任何减轻都会产生巨大的影响。 根据材料的选择,3d打印零件可以比用钢和铝制造的传统零件轻得多。在拥有340多个独特3d打印部件的xb-1上,重量的减轻带来了巨大的不同。 现在,制造团队已经将xb-1交付给地面和飞行测试团队,他们正将注意力转向overture的设计和制造,这是boom未来的超音速客机。对于overture来说,3d打印的可能性似乎是无穷无尽的,除了原型设计、加油和飞行硬件外,还可以选择机舱内部、飞行甲板和厨房的3d打印部件。3d打印的进步为这些可能性提供了动力,这将为降低生产成本、加快制造进度以及通过制造更轻的飞机来减少排放开辟新的途径。
了解更多

rp m 3d 打印了波音 starliner 航天器的座椅
3d打印服务局快速原型和制造(rp m)通过社交媒体透露,其俄亥俄州总部的一个工程师团队已经3d打印了波音starliner飞船使用的座椅,该飞船于19年2022月<>日在nasa的无人飞行测试中发射到国际空间站(iss),并在六天后安全返回地球。 “五月对rp m来说是一个繁忙的月份,”linkedin上的帖子写道。“我们很自豪能成为美国国家航空航天局(nasa)和波音公司这一具有里程碑意义的任务的一部分,该任务于19月<>日成功发射了星际客机,并于上周重新进入。增材制造『实际上』正在改变世界,朋友们! 此外,rp m 增材制造工程师 cameron rogers 不仅证实该公司是 starliner 3d打印座椅的幕后推手,他还表示 rp m 打印了“三套不同的座椅,尺寸略有不同”。 对于这项任务,rp m 依靠 stratasys 的熔融沉积建模(fdm)技术,该技术与专用3d打印机和生产级热塑性塑胶配合使用,以制造坚固、耐用且尺寸稳定的部件。具体来说,stratasys fdm 的商业负责人 tom leach 表示,该团队使用了 f900大型体积打印机和 ultem 9085 树脂3d印表材料来制造座椅。 美国宇航局宇航员观看联合发射联盟阿特拉斯五号火箭与波音公司的cst-100 starliner航天器在轨道飞行测试-2任务之前被推出到发射台。图片由nasa/joel kowsky提供。 由波音公司制造的乘员太空运输(cst)-100 starliner是一类两艘部分可重复使用的航天器,旨在将乘员运送到国际空间站和其他低地球轨道(leo)目的地,作为航空航天巨头对nasa商业乘员计划的贡献的一部分。与spacex一起,波音公司的任务是建造一艘航天器来取代航天飞机,并使美国摆脱长达十年的依赖俄罗斯联盟号太空舱进入轨道站。 spacex 在9年乘坐猎鹰 2020 号火箭发射首次载人任务后取得了进展,现在定期将机组人员送往国际空间站。然而,波音公司在试图让starliner启动并运行实际的载人任务时遇到了一系列问题。 最后一次试飞被称为轨道飞行试验2(oft-2),是 oft-1 测试的重做,该测试于2019年发射,但在 starliner 因软件逆境导致太空舱在发射后不久烧毁推进剂而发生故障,未能到达国际空间站后过早结束。 波音公司解决了这些问题,并让starliner准备好在2年夏天在 oft-2021上发射,但在计划升空前不久的飞行前检查显示,太空舱服务模块推进系统上有13个卡住的阀门没有回应命令。路透社最近的一份报告称,由于aerojet rocketdyne是starliner服务模块推进系统的官方硬件供应商,两家公司因燃油阀故障而发生冲突。 从那时起,波音公司花了大约八个月的时间来解决导致航班延误的问题。一旦航天器上的阀门问题得到解决,oft-2终于起飞了。这对rp m团队来说是个好消息,他们终于在轨道上见证了3d打印座椅。 座位上是「火箭人罗茜」,这是波音公司的人体测量测试设备,以二战的铆工罗西命名,是对在航空航天和人类航天领域开辟道路的女性的颂歌。罗茜被绑在starliner上进行飞行测试,这次是为了帮助航天器在飞行的各个阶段保持重心。 “她是一个 180 磅重的欧洲棕褐色测试设备,旨在代表人类身高和体重尺寸的第 50 个百分位,”商业船员计划船员和货物住宿子系统负责人 melanie weber 说。“罗茜的第一次飞行提供了数百个关于宇航员在飞行过程中将经历的数据点,但这一次她将帮助保持starliner在上升、对接、脱离和着陆过程中的重心。即使是你驾驶的汽车也必须保持重心,否则它可能会翻车。 对于oft-2,先前连接到rosie的15个传感器的航天器数据捕获埠用于从放置在座椅托盘上的传感器收集数据,座椅托盘是将所有乘员座椅固定到位的基础设施。传感器可以捕获数据,以表征所有四个乘员座椅的运动,乘员舱总工程师dan niedermaier解释说。 罗茜穿着波音蓝色宇航服和红色波点头巾,还戴着由95岁的梅·克里尔(mae krier)手工缝制的配套口罩,梅·克里尔(mae krier)是现实生活中的罗茜,她17岁时在西雅图的一家波音工厂帮助制造飞机。 starliner 人体测量测试设备 rosie the rocketeer 在 starliner 太空舱的轨道飞行测试 19 期间戴着手工缝制的 rosie 主题 covid-2 口罩和亲笔签名的 rosie 围巾。图片由波音公司提供。 波音公司与美国宇航局的合同涵盖了无人驾驶的oft-1和oft-2任务,以及预计将于今年年底或明年初与两名宇航员barry “butch” wilmore和suni williams一起发射的机组飞行测试。第一次载人试飞将从佛罗里达州卡纳维拉尔角太空部队基地的太空发射场-41乘坐联合发射联盟阿特拉斯五号火箭升空,就像oft-2一样。 一旦试飞完成,美国宇航局将开始对starliner航天器和系统进行认证,以执行空间站的载人任务。定期、长期的商业船员轮换任务使该机构能够继续在轨道实验室上进行研究和技术调查,并为未来探索月球和火星奠定基础。 作者:vanesa listek3d打印机3d打印3d打印材料太空3d打印
了解更多

案例|agile space industries:通过增材制造和 3dxpert 推动太空探索
自人类首次登上月球以来已经过去了半个多世纪,月球任务仍然是一项充满挑战的任务。但随着 3d 打印技术为快速产品开发和新颖的质量减轻方法打开了大门,太空探索得到了新的推动。如今,增材制造公司是月球任务中的宝贵盟友。 client agile space industries location 美国 challenge 批量化3d打印推进器和火箭发动机 其中一个例子是太空推进凯发k8官网的解决方案提供商 agile space industries。该公司总部位于美国,生产推进器和火箭发动机,提供从设计、3d 打印服务、减材制造到测试能力的一切服务。 他们的客户包括像 astrobotic 这样的月球探索公司,其 griffin mission one 计划于 2024 年向月球南极运送 nasa 漫游车,以及旨在数据准备可持续的地球和月球生态系统的 ispace。以及其他几个月球任务。 增材制造是火箭推进器和发动机的完美制造方法。“对于太空应用的发动机部件,重量是一个重要因素,”agile space industries 的高级增材制造工程师达斯汀·克劳斯 (dustin crouse) 表示:“增材制造为设计空间带来了无限的可能性。它使我们能够大幅减少质量并快速迭代新设计。” 公司依靠 agile space 快速获得最先进的凯发k8官网的解决方案。“我们可以在几周内完成从设计、制造到组装和热火测试的整个过程。传统上,完成一次设计迭代需要数年时间,”克劳斯解释道。“我们的工程师发布设计两天后,我们就可以制造竣工零件。这真是令人难以置信。” agile 使用 oqton 的工业 3d打印软件 3dxpert 来高效生产 3d 打印零件。 确保生产的可追溯性 事实证明,该软件对于保持数据准备之间的一致性至关重要。当开发工程师将零件交给生产工程师进行数据准备准备时,最好的做法是“锁定”一组参数并限制可以更改的内容,以确保零件保持不变。 在agile,生产工程师在“操作员”环境中获取文件,这是一个他们可以移动零件、删除组件和更新序列号的工作空间,但其他软件功能被锁定。“这使我们能够将数据准备准备工作交给操作员,而不必担心他们可能会意外更改零件的打印方式,”克劳斯解释道。 使用操作符还可以节省重新切片的时间。“当您在常规 3d 打印环境中更新序列号时,您必须重新切片零件 - 这可能需要几个小时。在 3dxpert 中,您可以在操作员环境中打开已切片的零件,只需重新切片零件标签即可。只需几分钟,”他补充道。 “我们目前正在研究需要一个半小时才能切片的大型部件。如果每次更改序列号时都必须迭代并重新切片整个组件,则需要额外的一个半小时。使用oqton系统,只需几分钟,”克劳斯解释道。 切片并忠于设计 agile space industries 增材制造总监 kyle metsger 指出了 3dxpert 为其切片流程带来的多项优势 - 节省时间、消除可变性和降低硬件要求。这些源于一项功能:使用3d打印机指定格式,对三维模型进行切片计算。 其他 3d 打印软件需要用户将模型转换为 stl 文件才能进行切片。这曾经给 metsger 带来了许多操作难题,其中最大的问题之一是对原始几何形状的转换误差。 “我们的每一个组件都具有精细的通道、精细的特征和严格的公差。当您采用 cad 模型并将其转换为 stl 时,您会创建原始几何形状的近似值、这个会带来误差。由于我们正在打印直径数千的孔和通道,因此尺寸变化很难控制。”metsger 解释道。 " 转换为 stl 会导致几何图形出现偏差,这也意味着您正在以未知的方式重新定义特征。这是一种风险,但我们在 3dxpert 中根本不需要处理这种风险" benjamin graybill senior additive manufacturing engineer, agile space industries 修复 stl 是可能的解决方法,但根据 metsger 的经验,编辑客户几何图形很难确保完全满足法规要求。 agile space 的高级增材制造工程师本杰明·格雷比尔 (benjamin graybill) 强调,变化会导致其他重大问题。“转换为 stl 会导致几何图形出现偏差,这也意味着您正在以未知的方式重新定义特征。这是一种风险,但我们在 3dxpert 中根本不需要处理这种风险,”他说。 “我们所有的产品都是性能驱动的,但性能本质上来自于功能。我们越忠实地数据准备这些功能,即使在精细的分辨率下,我们就越能代表设计,”格雷比尔补充道。 快速数据准备 最大的改进之一是切片时间、硬件要求和小文件大小。 由于许多内部功能和高分辨率,agile space industries 制造的许多组件都有一个非常“强大”的 cad 模型。复杂的 cad 几何形状会产生大型 stl 文件。大的 stl 文件需要大量 ram。 “当您将我们的一个 cad 模型转换为 stl 时,它可能会达到 1 gb 或更大。该大小的文件的硬件要求逐渐增加。我们曾经遇到过这样的情况:在数据准备软件中移动文件,并且加载需要 20 分钟。在 3dxpert 中,您可以对原生 cad 模型进行切片,并且 ram 要求要小得多,”metsger 解释道。 当他们在没有 3dxpert 的情况下打印 4 英寸推进器喷射器组件时,数据准备需要 14 小时,并且 stl 文件中存在 1 到 5 微米的偏差,具体取决于分辨率。 这对他们的工作流程产生了重大影响。“我们过去常常在工作日进行数据准备,然后让计算机通宵运行来对文件进行切片。我们无法在同一天打印该零件。借助 3dxpert,我们发现从数据准备准备到机器的总时间减少了 60% 到 70%。”metsger 补充道。 " 我们过去常常在工作日进行数据准备,然后让计算机通宵运行来对文件进行切片。我们无法在同一天打印该零件。借助 3dxpert,我们发现从数据准备准备到机器运行的总时间缩短了 60% 到 70%。" kyle metsger director of additive manufacturing, agile space industries 两个生产基地,一个数字线程 3dxpert 的另一个重要优势是可以轻松地为在不同位置运行的项目创建单个连续的数字线程。 agile space industries 在宾夕法尼亚州芒特普莱森特和科罗拉多州杜兰戈的两个工厂生产零部件。格雷比尔认为,两个站点之间的顺畅通信和文件传输是其运营不可或缺的一部分:“当您创建关键任务组件时,即使是数字线程中的小错误也是不能容忍的。我们需要在整个制造过程中建立一条无懈可击的数字主线。”他解释道。 “3dxpert 软件减少了数字线程中的痛点和瓶颈。将我们所有的数据准备工作集成到一个软件中,我们简化并减少了转换过程或团队之间简单交接中发生错误的可能性。”graybill 补充道。 客户服务成功:trunprint 金属3d打印机和3dxpret集成 总体而言,agile 的增材团队发现 3dxpert 的功能优于其他 3d 打印软件,因此他们决定在正式集成之前将其应用到所有四台 trumpf truprint 机器上。 他们与 3dxpert 团队携手合作,从头开始数据准备 truprint 1000、2000 和 5000 处理环境。“我们从请求 3dxpert 帮助将软件与我们的机器集成到在几周内全面实施。这不仅证明了他们的技术专长,也证明了他们对客户的价值。”克劳斯补充道。 如今,3dxpert 和 truprint 集成 提供了无缝的增材制造工作流程,使更广泛的组织能够进行工业规模的 3d 打印。 但关系并没有就此结束。agile 和 3dxpert 团队定期会面讨论用户驱动的改进。crouse 赞扬 3dxpert 的客户服务,“软件提供商并不经常与其客户进行个人接触。如果我打电话,他们就会接听。我可以信赖 oqton 团队会认真对待我的要求,这体现在我们所看到的持续流程改进中。” agile space 认识到他们只触及了 3dxpert 功能的表面。他们相信与 3dxpert 的合作将使他们能够快速实现新功能,并为他们提供超越竞争对手的领先优势。 关键要点 节约 60%~70% 3d打印数据处理时间 通过直接从 cad 模型进行切片来避免设计——制造误差 压缩复杂推进器模型数据的大小
了解更多

海洋、陆地和天空:3d打印如何影响交通
ultimaker制造系列。3d打印使整个运输部门能够实现快速原型设计和更高效的制造。 3d打印 -增材制造 -运输 在这篇ultimaker支持系列的第四篇文章中,我们将探讨运输行业利用这项技术的多种方式,从快速原型设计到制造辅助工具再到最终用途零件,以及未来的发展趋势。我们之前的两篇系列文章主要关注制造业和包装业。 自3d打印技术问世之初,航空和汽车等运输行业就与3d打印联系在一起。为了让你了解这些联系的深度,汽车公司——比如购买了首批3d打印机之一的福特——和航空航天公司是20世纪80年代末3d打印的首批投资者和采用者之一。 当时,3d打印代表了一种新的凯发k8官网的解决方案,可能会破坏零件的设计和原型。如今,随着运输业继续积极采用增材制造,利用该技术的独特能力来生产优化设计,加快产品开发,提供具有成本效益的低批量制造,并支持制造工作流程和供应链,这一潜力和更多潜力已经实现。 在添加剂发展的这个阶段,这项技术只代表了运输行业整体价值的一小部分。例如,2021年,全球汽车制造市场估计价值2.86万亿美元[1];据计算,2022年汽车增材制造业约为29亿美元[2](约占汽车市值的0.10%)。但是,随着采用率的提高、流程自动化的提高以及新应用程序的验证,am在运输中的价值正在稳步增长。例如,在航空航天领域,即使在新冠肺炎封锁导致经济放缓之后,增材制造市场仍在稳步增长,预计2028年将超过130亿美元(2021年为37.3亿美元)。[3] 这种增长在所有运输行业都是如此。 加快产品开发 增材制造现在广泛应用于许多行业,用于原型设计和产品开发。运输业也不例外。在汽车、航空和铁路领域,3d打印机使工程师和设计师能够快速、经济高效地打印、测试、调整和验证新设计。至关重要的是,物理3d打印原型使运输制造商能够轻松地回到绘图板上,在不显著增加周转时间的情况下克服设计缺陷(部分归功于3d打印机能够昼夜无人值守地制造零件)。这意味着,不仅可以更快、更便宜地将新设计推向市场,而且可以在产品开发周期的早期发现缺陷,从而降低重大检修和昂贵产品召回的风险。换句话说,3d打印解锁了更好的产品设计。 熔融丝制造(fff)系统,如ultimaker的系统,特别适合功能原型设计。ultimaker打印机可以容纳多种材料,从标准细丝到工程级复合材料。这种多功能性使工程师和产品设计师能够打印出与最终零件特性非常相似(甚至匹配)的原型,从而促进功能测试和验证过程。 eventuri宝马m4的3d打印进气原型。图片来源:ultimaker。 eventuri为奥迪rs系列和m-power宝马等高性能汽车制造进气系统,3d打印现在是其产品开发过程中不可或缺的一部分。该公司依靠ultimaker 3d打印机将数字进气管模型快速转换为可以测试功能和贴合度的物理原型。如果性能不足或不太合适,eventuri工程师可以简单地在cad软件中调整设计并重新打印以进行验证。不用说,这种灵活且完全内部的工作流程为公司节省了时间和金钱,并使其能够开发出卓越的进气设计。 运输中的制造效率 如果你看看今天运输行业的生产线,你很有可能会遇到一个或多个3d打印组件。该技术越来越多地被用于通过开发夹具、装配夹具、质量控制工具和更换零件来提高生产环境的效率。在这种情况下,fff 3d打印提供了许多独特的优势:它有助于现场按需生产(从而最大限度地减少机器停机时间);它不需要工具;这是一种用户友好的技术,生产线操作员和工程师可以轻松掌握;它能够开发出更高效、更符合人体工程学的生产辅助工具,从而提高生产效率和安全性。 特别是在汽车行业,制造商已经通过内部采用fff 3d打印来改变他们的生产流程。例如,大众汽车现在使用ultimaker 3d打印机生产其绝大多数制造工具。在使用3d打印之前,这家汽车公司依靠外部制造商制造制造辅助工具和工具,通常需要数周时间才能交付。然而,通过内部3d打印,大众汽车autoeuropa将工具开发时间缩短了95%,成本降低了91%。 大众汽车欧洲工厂的3d打印举升门徽章每件仅需10欧元。图片来源:ultimaker。 大众汽车有很多3d打印制造工具的例子,包括用于正确定位汽车徽章的举升门徽章。该零件过去每台售价400欧元,周转时间为35天,现在只需4天就可以在内部制造,每台售价仅为10欧元。总之,这家年产量为10万辆汽车的汽车制造商现在有能力按需开发和实施工具,以保持其生产线的平稳和安全运行。 提升最终用途零件 添加剂技术在最终用途零件的运输中也产生了巨大影响。这一应用领域主要由3d打印的设计自由度及其可扩展性驱动,这使得前所未有的几何形状得以实现。在设计方面,3d打印提供了一种创建以前不可能的几何形状的方法,例如有机形状和内部空腔和通道等特征。它还允许零件合并,从而最大限度地减少组装时间,通常还可以减少零件重量。从可扩展性来看,3d打印是低批量生产的最佳制造工艺之一。这对航空航天行业来说是一个巨大的吸引力,因为航空航天行业通常需要较小规模的高度复杂零件生产。然而,扩大生产也是可能的:它只需要添加更多的3d打印机单元。 该技术的设计能力在运输领域尤其有价值,在运输领域,将更轻的部件集成到车辆中是提高燃油效率的关键。例如,在航空领域,通用电气的faa认证ge9x发动机集成了300多个3d打印零件,包括整合的燃料喷嘴尖端。与以前的发动机系统相比,这些印刷零件的轻质设计使燃油效率提高了10%。[4] 在汽车领域,3d打印也用于最终用途的生产,尤其是在需要小批量或定制的情况下。美国汽车修复服务公司tucci hot rods定期使用3d打印为客户生产定制汽车零件。这家家族企业依靠3d打印机(包括两台ultimaker机器)及时、经济高效地制造汽车改装,如3d打印仪表板。得益于这项技术,该公司的生产速度提高了两倍,并节省了高达90%的成本。在sema 2022上,该公司推出了一款2021款福特maverick,该车集成了大量由petg制成的3d打印部件,包括挡泥板、制动管、尾翼等。[5] 每个印刷零件在组装前都经过后处理,从而形成了一辆独特的紧凑型卡车,利用了am的定制能力 ultimaker的金属fff功能也被证明在运输领域具有价值。如今,该公司的可访问金属3d打印功能有很多例子(可能得益于ultimaker s5、金属扩展套件和巴斯夫ultrafuse®不锈钢丝的组合),使运输制造商能够生产最终用途的部件。设计和制造柴油发动机的利勃海尔组件colmar sas公司为了节省时间和金钱,转而使用金属fff生产发动机支架。这个零件只需要有限的数量,最初在数控加工时花费102美元,需要很长时间才能制造出来。在验证了金属fff的应用后,利勃海尔组件公司优化了支架的设计,使最终组件的承载能力是机加工支架的三倍,质量比机加工支架减少了60%。印刷零件还将成本降低了近一半,并显著加快了交付周期。 这只是众多案例中的一个。川崎汽车公司为摩托车设计零件,现在用巴斯夫ultrafuse®17-4ph 3d打印换档杆 不锈钢。这些零件比铝制零件更耐腐蚀,而且成本效益更高。除此之外,这家摩托车制造商现在可以为不同的骑手定制换挡杆。schwartz off-road motorsportz(sorm)在生产其独一无二的sxs pro mod赛车时也使用了金属fff。具体来说,它将支架组件从碳纤维尼龙升级为17-4ph不锈钢。金属fff使sorm能够定制零件并实现更大的耐温性。 未来创新的机遇 如果我们看看交通运输的当前趋势,特别是汽车行业的趋势,很明显,3d打印是推动这些趋势的关键技术之一。例如,增材制造被积极用于电动汽车的开发,用于原型设计和生产零件,包括必须紧凑并设计为最佳匹配的电池外壳。电动汽车还从3d打印实现的轻量化中受益匪浅,因为重量会影响电池里程。[6] 3d打印的最终用途零件。图片来源:ultimaker 3d打印在高性能超级汽车的开发中也至关重要。在超级汽车制造商briggs automotive company(bac),ultimaker的s5生态系统是其最新车型mono r的开发和生产的核心。据该公司称,mono r超级跑车集成了44多个3d打印零件,包括结构发动机部件、翼镜支架和灯围。该技术使该公司能够测试其高性能汽车的新设计并探索创新凯发k8官网的解决方案。正如bac的设计总监兼联合创始人ian briggs所说:“ultimaker生态系统使我们能够将生产的所有不同方面结合在一起,不断优化并存储在一个位置。” 建立更可持续的做法和循环经济也是运输业更加重视的一个关键优先事项。正如我们所看到的,3d打印通过生产更轻的零件在这方面起到了帮助作用。但运输公司也有追求可持续发展的途径。 以荷兰航空公司荷兰皇家航空公司为例,该公司通过将航班上的pet水瓶改造成3d打印细丝,在创造循环经济方面取得了长足进步。这种细丝用于生产功能部件,如发动机叶片风扇罩,在喷砂过程中保护发动机叶片的零件。这一过程为风机叶片表面的各种处理做好准备,如油漆去除和涂漆、除油和除锈以及一般清洁。通过使用ultimaker系统和回收灯丝,荷航能够高效、可持续地生产这些功能部件。[7] 铁路和海运等其他运输部门正越来越多地意识到附加技术的潜力。多亏了am,列车mro服务和德国铁路和öbb等铁路公司现在能够对难以或不可能采购的列车部件进行逆向工程和3d打印,从而缩短了列车的停机时间。[8] 越来越多的可用材料,包括高温热塑性塑料和阻燃丝,再加上ultimaker等开放材料平台,也为功能性铁路和运输部件创造了新的机会。例如,在奥地利铁路公司öbb,工程师们目前正在评估使用ultimaker系统和ultrafuse不锈钢丝制成的3d打印不锈钢部件的概念验证。这家铁路公司还采用添加剂凯发k8官网的解决方案来简化其供应链,这得益于及时生产,并最大限度地减少库存和运输需求。 在海运行业,据说该行业占世界贸易的80%以上[9],3d打印有可能支撑脆弱且低效的零部件供应链。在这方面,wilhelmsen航运公司率先开发了一个认证备件的数字库存,该库存可以打印在船上进行现场维护,也可以在最近的港口打印,以缩短更换零件的交付周期。[10] 这种方法缩短了供应链,不仅简化了备件的采购方式,还通过减少运输排放来提高可持续性。 在所有运输行业中,3d打印的实施正在释放效益和效率,包括缩短交付周期和加快上市时间;更大的生产灵活性和工厂生产线的增加;提高设备效率和操作员的安全性;精简业务和缩短供应链;以及更高效的仓储和库存操作。 结论 从海洋到天空,像ultimaker的fff生态系统这样的3d打印凯发k8官网的解决方案正在帮助改变所有运输行业。汽车、航空、铁路和海事领域的工程师、原始设备制造商和mro正在其运营中体验3d打印的好处,并不断探索利用该技术缩短交付周期、节省成本和开发新创新的新方法。 参考文献 1.2019年至2022年全球汽车制造业收入[互联网]。statista。2023年8月28日。可从以下位置获得:https://www.statista.com/statistics/574151/global-automotive-industry-revenue/ 2.汽车3d打印市场:2030年趋势预测[互联网]。delvens。2023年1月。可从以下位置获得:https://www.delvens.com/report/automotive-3d-printing-market-trends-forecast-till-2030 3.到2021年,航空航天和国防增材制造市场价值将达到1301亿美元[互联网]。财富商业洞察。2022年3月30日。可从以下位置获得:https://www.globen
了解更多

aitiip使用nexa3d自由注射成型方案,制造高性能碳填充peek部件替代金属零件。
aitiip是西班牙领先的研发机构,为航空、自动化、工业和包装领域的公司提供服务。该研究所拥有强大的材料和工艺表征平台,并被称为强大的技术集成商,不断寻找下一个变革技术。半年前,aitiip实施了nexa3d的nxe 400pro 3d打印机平台,以探索增材制造和注塑成型的集成。 liebherr是德国领先的工业设备制造商,以其图卢兹航空分公司为代表,与aitiip合作,以实现用回收注塑高性能聚合物制造的法兰轮取代金属法兰轮的目标。他们的目标是:开发一种技术,允许使用100%可回收材料制造用于航空冷却系统的法兰轮。认识到所选聚合物的性能对质量至关重要,并且通过增材制造实现某些部件特征将更具成本效益,aitiip转向nxe 400和freeform注射成型,以满足客户的期望。挑战再生peek材料性能要求和高复杂度 在大多数制造过程中,复杂性是成本增长因素,制造商一直将增材制造视为简化复杂物体制造的一种方式。在法兰轮的情况下,设计复杂性的挑战与用碳填充peek取代金属的野心相结合,peek是一种高性能热塑性塑料,众所周知难以成型。在制造peek零件时,需要严格控制工艺参数以实现目标性能,liebherr与aitiip合作开发并验证了满足以下要求的制造工艺:1. 高速制造工艺将使成本降低30% 2. 100%可回收材料 3. 轻量化—减轻40%的重量 4. 快速制造 “nexa3d打印机和xmold树脂提供的质量、可重复性和自由度使我们能够实现一种全新的按需制造模式。” – pablo murillo, aitiip 凯发k8官网的解决方案 优势 测试并验证了金属更换 通过小批量注塑成型实现备件需求 不需要对金属工模具进行投资以进行早期的性能验证 增材制造与注射成型的整合 要制造的零件是一个结构复杂的法兰轮,具有挑战性的载荷情况。为了达到要求的零件性能和制造速度,选择了注射成型的制造方法。然而,法兰轮的复杂性传统金属模具无法实现。 为了满足liebherr的要求,aitiip决定以高度创新的方式充分利用nxe 400pro系统的功能: 使用nexax pro软件,atiip创建了一个独特的打印机配置文件,以实现具有卓越表面质量的零件。 叶轮体内部复杂几何形状是通过nexa3d 打印xmold模具树脂,后期溶解来实现 一个特殊的部件功能是通过使用nexa3d xpeek材料打印的插入件实现的,该插入件在注射前安装在可溶插入件中,从而使其完全集成到注塑叶轮部件中 具有xpeek功能的3d打印插入件安装在模具腔中。随后,注入碳增强peek材料填充空腔,并溶解3d打印的xmold插入件,释放最终的peek部件。 peek材料复杂叶轮按需生产 nexa3d自由注射成型,结合高性能的xpeek镶件,使atiip能够满足制造高性能的可回收注射成型peek金属替换件。此外,aitiip可以在投资模具之前验证零件的性能。 早期验证:使用3d打印xmold树脂模具使atiip能够制造许多测试部件,并使用这些部件验证关键的设计和性能。 节省成本和时间:自由注射成型允许aitiip每周迭代,因此与传统的模具制造工艺相比,减少了项目时间,达到了更好、更先进的结果。此外,研究成本大幅降低,使更有效地利用资源,同时增加了设计的自由度。 无缝可扩展性:第一次迭代是在较小的3d打印模具中进行的,以确保以最低的成本进行最短的迭代。一旦零件设计得到验证,atiip就开始实施金属腔,以降低单位成本,同时仍然使用3d打印的xmold芯和xpeek插入件,以避免在复杂的滑块功能上进行昂贵的投资。 快速迭代:快速且经济有效地测试大量模具概念的能力是项目最终成功的关键因素。该部件的复杂设计,加上碳填充peek的复杂加工,再加上将3d打印的xpeek插入件集成到注塑件中的额外挑战,由于涉及大量投资,因此使用传统的金属模具来实现该项目非常困难且成本高昂。 源文摘自: nexa3d
了解更多

inn-paek项目成功实现100%可回收涡轮机
欧洲项目将飞机冷却系统中复杂形状的金属结构替换为注射成型的热塑性复合材料,以提高可持续性。 碳纤维增强paek复合材料涡轮叶轮和法兰在内paek项目中得到验证。图片来源:inn-paek项目,aitiip技术中心 aitiip技术中心(西班牙萨拉戈萨),与利勃海尔集团(瑞士布勒),已经完成了三年的欧洲paek酒店并取得了可喜的科技成果。顺时针方向的行波(continuous wave)报告项目的目标2023年1月。aitiip现已成功开发出一种创新的专利技术,能够使用热塑性复合材料和一次性注射工艺生产复杂几何形状的零件。 inn-paek公司通过制造用于飞机冷却系统的涡轮机成功地展示了这些材料和工艺。aitiip报道说,这是一个革命性的演示器——到目前为止,只使用金属材料。相比之下,用碳纤维增强的热塑性聚合物复合材料具有重量轻、机械性能高、耐腐蚀、耐潮湿和耐化学品以及多功能性提高等优点。它们还可以在零件使用寿命结束时回收,并重新用于制造新零件。 inn-paek的技术凯发k8官网的解决方案使得用有利于“一次成型”生产的注射成型工艺取代当今金属涡轮机的传统制造工艺成为可能,在传统制造工艺中,各种零件被焊接在一起,从而优化了周期时间、能源消耗并降低了成本。aitiip采用了这种注射工艺,以适应生产这些飞机冷却涡轮所需的特殊和复杂的几何形状,同时使用了重量更轻、更可持续的结构。 inn-paek能够展示材料和工艺,以实现40%的重量减轻和30%的成本降低,并提高最终零件的吸声性能。该项目的成果是作为一种先进的、更可持续的和环境友好的生产系统提供的,未来的航空业可以从中受益。欧洲正在将这一行业重新导向循环,这将要求在未来几年内使用替代结构和部件来实现降低燃料消耗和二氧化碳排放的目标2排放量减少20%。据估计,未来20年将需要约40,000架新飞机来满足运输需求。 inn-paek的研究已经从欧盟地平线2020框架计划内的清洁天空2联合项目(现称清洁航空)获得了近80万€的资助。 源文摘自:compositesworld
了解更多

fdm成功案例 –飞机起落架设计
使用机种: uprint 地点:台北树林 前言: 起落架是航空器下部用于起飞降落或地面(或水面)滑行时支撑航空器并用于地面(或水面)移动的附件装置。 目前大部份飞机都是采用前三点式起落架,起落架有一组鼻轮和两组主轮支撑整个飞机,飞机重心位于主轮之前。前三点式起落架比后三点式起落架最大的优点是前者能使飞机处于水平或接近水平的状态,当飞机在地面时不会影响飞行员的视野,喷射发动机所排出的高温废气不会因为飞机不是处于水平状态而直接喷向跑道铺面,对跑道的负面影响较少。 起落架是惟一一个支撑整架飞机的部件,因此它是飞机不可分缺的一部份;没有它,飞机便不能移动。当飞机起飞后,可以视飞机性能而收回起落架。 任务挑战:缩短机构设计验证时间 比例飞机机种繁多,需要频繁地进行不同款式机种的起落架设计。 需要实体验证飞机起落架机构设计,包含放出与回收的动作。 面对市场竞争,客户需要更快速的工具来完成验证。 希望使用材料强度好的快速原型成品,满足少量多样及耐候的需求。 需要快速设计各种理论的机构进行反覆测试。 凯发k8官网的解决方案:fdm工程材料快速原型制造系统 图 比例喷射飞机原型一 图 比例喷射飞机原型二 图 比例螺旋桨飞机原型三 图 起落架展开示意 图 起落架展开示意 图 起落架收合示意 图 局部放大图 图 局部放大图 图 局部放大图 图 局部放大图 图 局部放大图 图 整体组装 设技师指出fdm工程材料快速原型制造系统优势: 机构元件所使用的fdm abs工程材料,具有高强韧性、耐候不变形的特性,非常适合进行少量生产制作,工件可以组装测试机构使用。 对于设计人员而言,与传统cnc相比,不需要任何加工经验与技术,即可再计算机旁快速输出各种机构设计元件,不受加工程序限制。 大幅缩短设计变更时间,上午设计变更完成,下午就能进行测试。
了解更多

用户故事|amt :非接触式航空航天零件验证将首件检验时间缩短了一半
供应链上的延误对制造业的影响与高速公路车道关闭的影响相同。这一点在质量检验中最为明显。 “设计、分析、机床和刀具技术方面更好的流程极大地提高了制造可靠性和速度,但质量检验仍然落后,” aerospace manufacturing technologies (amt)首席执行官 matt reinhard 表示:“制造业拥有消防水带能力,但质量检验却将其限制为毛毛雨。” “更快的响应时间至关重要,虽然 cmm 很准确,但成本高、速度慢以及与 3d cad 模型关联的困难使得它们不太利于在制造过程中进行调整。像波音这样的客户受到设备制造商的压力,因为他们试图削减库存,我们需要减少制造检查阶段的时间。” matt reinhard amt ceo 设计检测新思路 amt 为航空航天工业制造各种尺寸的 3 轴、4 轴和 5 轴铣削零件、拉伸成型零件和钣金零件。该公司最近转向使用非接触式激光扫描和计算机辅助检测软件来加快首件检验效率。amt 使用传统的坐标测量机 (cmm) 进行最终质量检查。 “显然,质量是航空航天制造的一大关注点,”reinhard说。“现在,速度的压力促使我们采用了新的检查流程——我们希望该流程能够在全行业范围内实现标准化。” amt 的新流程从 metron systems 的 msg2 扫描仪开始,该扫描仪将制造的零件捕获为高度详细的 3d 点云。msg2 是一个 18 x 26 英寸的立方体,允许 amt 将准备检查的零件放置在旋转台上,并以高达每秒 5,000 个点的速度进行扫描。如果零件对于立方体来说太大,则可以在更大的区域中移动和配置扫描仪以捕获必要的点。 扫描过程中捕获的大量点使 amt 能够快速准确地仔细检查复杂的轮廓、形状、形状和孔。这是相对于 cmm 的一个主要优势,cmm 只能扫描 30 到 40 个点,而 msg2 需要扫描数千个点。reinhard 表示,metron 的系统完成扫描所需的时间大约是 cmm 的一半。 另一个主要优势是自动化:metron 扫描仪的自动控制和校准意味着不需要高技能的工程师来执行检查,而且 amt 也不会在两台价值近 275,000 美元的 cmm 上浪费宝贵的时间。 metron systems 首席执行官汤姆·克拉里 (tom clary) 表示,metron 的扫描仪还可以处理导致一些非接触式扫描仪出现问题的材料。 “amt 适用于高反射材料,这传统上是非接触式扫描仪的弱点,”clary 说。“我们的系统可以扫描铝和钛等材料,无需喷漆、除尘或其他改变方法。” 在实施 msg2 扫描仪之前,amt 的首次物品质量检查可能需要半天的时间来设置并运行数小时。通过改为非接触式零件验证并使大部分工作自动化,amt 在短短半小时内即可完成检查。实际检查可能只需要几分钟。amt 的 reinhard 表示,时间的缩短可以节省人力、降低成本,并增加设计变更的灵活性。 “更快的响应时间至关重要,”他说。“虽然 cmm 很准确,但成本高、速度慢以及与 3d cad 模型关联的困难使得它们不太利于在制造过程中进行调整。像波音这样的客户受到原始设备制造商的压力,因为他们试图削减库存,我们需要减少制造检查阶段的时间。” 零部件与cad数据的转换 amt 新检测流程的第二部分涉及处理制造零件的 3d 点云数据,并将其与相应的 3d cad 模型进行比较。为此,amt 使用 oqton 的 geomagic control (geomagic control x)软件。 amt 将客户提供的 cad 模型和 metron 扫描仪捕获的点云加载到 geomagic control 中。cad 模型和点云在 geomagic control 中自动对齐,并且彩色图描绘偏差。当 amt 对尺寸、基准、特征和其他质量因素进行图形比较时,软件会自动记录会话以用于报告目的。 amt 使用 geomagic control 报告帮助设计人员决定需要进行哪些更改、对其铣床进行更改或证明该零件适合进一步生产。报告可以采用 html、pdf、microsoft word 和 excel 格式,以便打印或在线使用以进行协作评估。 在幕后,msg2 扫描仪和 geomagic control 在首次检查特定零件时收集的信息模板允许对同一零件进行后续检查,而无需进行新的设置。amt 正在利用这一功能开发一个包含 200 个不同零件检测配置文件的库,以进一步实现流程自动化。 “一旦该库实现,我们将能够将零件放在 metron 扫描仪上,点击条形码,然后自动扫描零件,”reinhard 说。“geomagic control 将从检查库中引入数据,然后在无需任何用户干预的情况下开发完成的检查报告。” “一旦该库实现,我们将能够将零件放在 metron 扫描仪上,点击条形码,然后自动扫描零件,”reinhard 说。“geomagic control 将从检查库中引入数据,然后在无需任何用户干预的情况下开发完成的检查报告。” matt reinhard amt ceo 获得认可 最终,metron 的 msg2 扫描仪和 geomagic control 软件可以超越首件检验和尺寸验证,涵盖整个质量检验流程。但就目前而言,reinhard表示,行业标准规定在将零件运送给客户之前使用坐标测量机进行质量检查。“我们的障碍是让客户熟悉我们用于首件检验的流程,”reinhard说。“通过创建非接触式零件验证的行业标准,节省宝贵的时间将改善供应链的流程,并减轻我们的客户在转向即时库存和其他成本节约措施时的压力。”
了解更多
zeiss 三维扫描仪 | 3d打印 普立得科技
普立得科技成立于2004年,专注于工业级3d打印机与三维扫描,同时我们也是zeiss gom代理商,并提供3d打印及扫描的代工整合服务,特此加值整合相关软体,包含拓扑优化设计 、医疗影像分析、逆向工程 、3d检测等,期望推进积层制造的使用习惯为生产带来更多价值。
深圳市福田区车公庙泰然四路天安创新科技广场大厦一期b座1208c (518040)
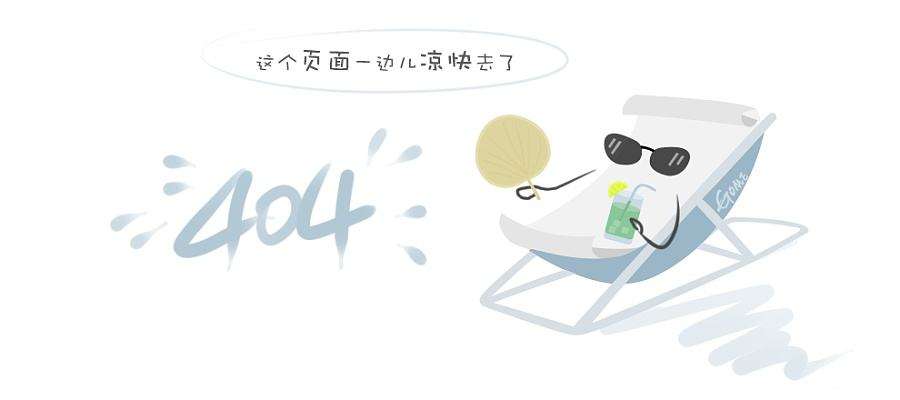
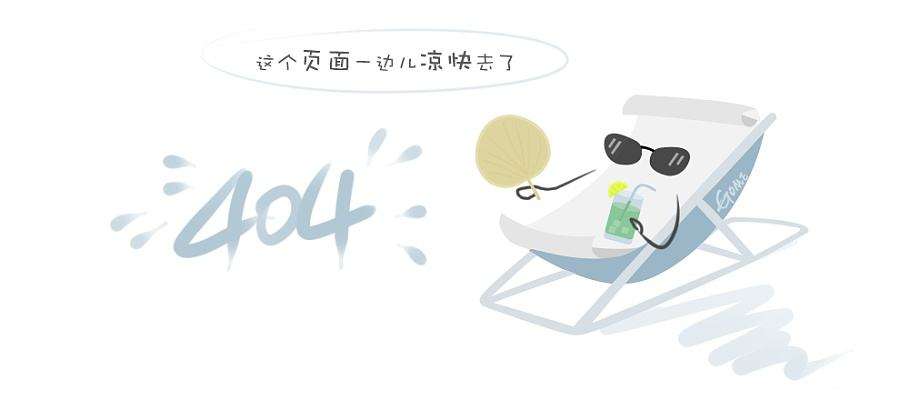
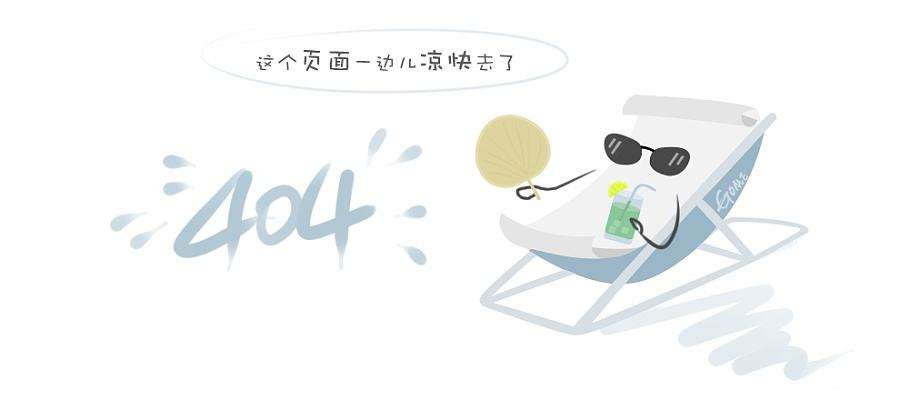
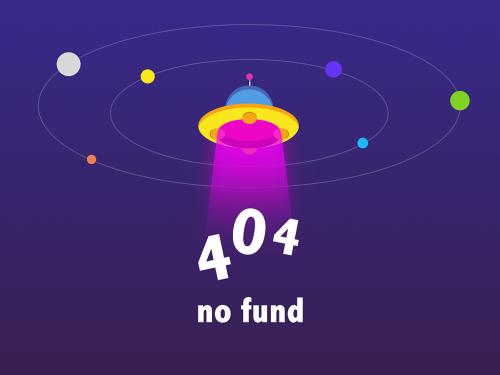
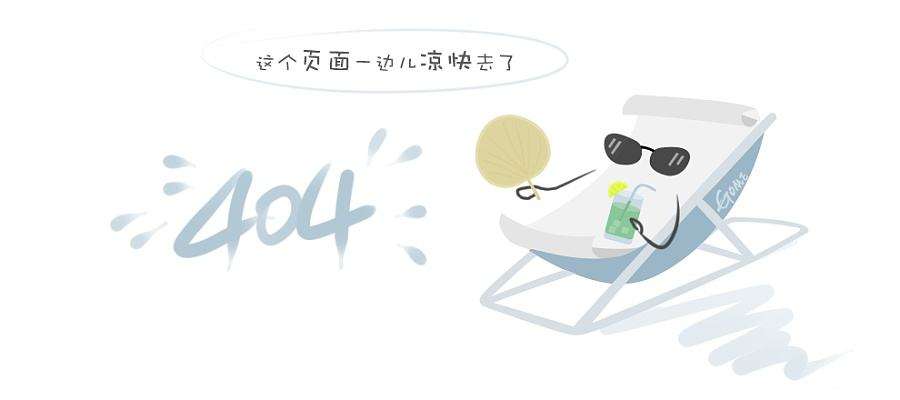
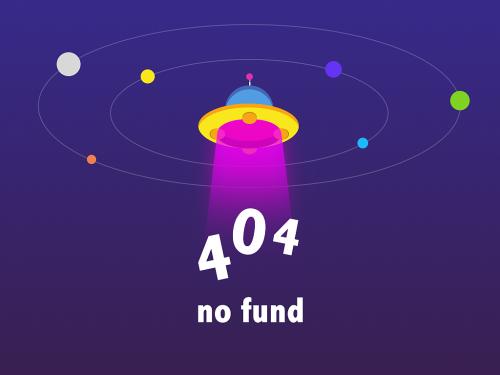
微信公众号
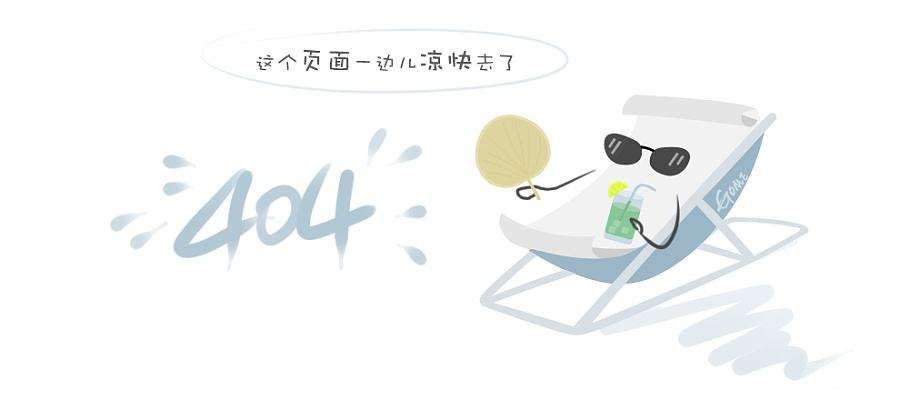
视频号
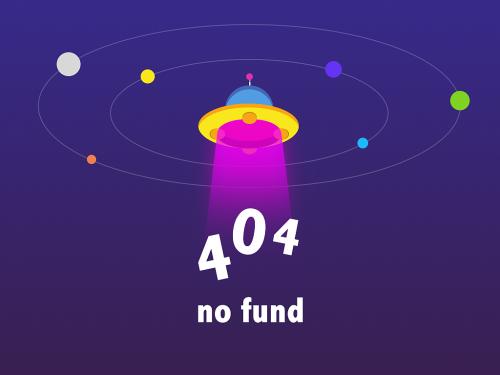
哔哩哔哩
您有什么疑问,或想咨询我们的产品与服务,请留下信息,我们会及时与您联系!